"40 years in bulk materials handling and the construction industry"

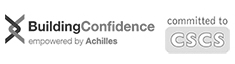
Based on the River Medway in Kent, Hanson’s replacement marine sand and gravel processing plant at Frindsbury Wharf is providing increased productivity withsignificantly reduced energy use. The operation supplies materials for concrete production such as 10, 20, and 40 mm aggregates including sharp washed sand to predominately ready mixed concrete outlets within a 20 mile radius, and also the Aggregate Industries bagging plant situated on an adjacent site.
The site was conceived in 1989 out of marshland and features a 200m cofferdam with a jetty that receives cargoes of sea-dredged aggregate from Hanson’s own fleet; predominately from the Norfolk coast and the English Channel. Hanson had been operating the old plant since March 1990. “It was basically mobile kit stuck up on stilts which corroded quite quickly,” says Mike Smith – Unit Manager at Frindsbury. The old plant was fed by a loading shovel, which carried materials to be processed 120 metres to the plant feed hopper with crushing of larger sizes involving mobile equipment. This meant that materials were first processed then stored, crushed and then processed again.
So five years ago, Hanson submitted applications for the current fully automated plant that eliminates the double handling. Planning was achieved a year later and the installation was completed in March 2009.
With the historic dockyards as well as residents just across the river, Hanson held an open day to explain the benefits that the new plant would deliver, such as less dust and noise and the fact that operation would no longer have to operate 24 hours a day due to its increased productivity. “Aesthetically, the site has improved tremendously,” says Mike. “Furthermore, it’s state-of-the-art in terms of conservation of electricity and conservation of water. From that we achieved planning quite quickly and we still kept the 24 operation ability in the unlikely event that this is required however it’s unlikely because the capacity of the new plant is substantially higher than the old plant.”
The old plant operated at approximately 150 tph; at its maximum the new plant will produce 550 – 600 tph, depending on operation mode and the material going through it. “Different dredging areas give a different make-up of the product we are trying to screen – from very fine to very course,” says Mike.
The principal contractor for the project was Centristic, who designed, manufactured, erected and commissioned the structures, chutework, hoppers, bins and conveyors, supplied the three Skako Comessa feeders and installed the free issue Sandvik crushers and screens. A Linatex sand plant and Haith thickener system were separately contracted to Hanson. The civils were designed by the Millward Partnership and constructed by Firgrove, while the electrics installed by IES.
The process operation
Various grades of raw marine aggregates are transported to Frindsbury by ship – 4500-5000 tonnes of product at a time – and ground stockpiled for plant processing. It takes about 4.5 hours to discharge around high water.
The Skako feeders can be run either manually or automatically,” explains Mike. “They can be run as a pair or individually. At the computer screen we can vary the percentage each feeder is working at the touch of the button on the computer control screen. This is how we blend the material.
The main feed is fed to a large scalpings screen where +100mm is rejected from the top deck to an external storage bay, whilst the lower deck screens +40 to 100mm clean stone for crushing and -32mm feed material to the wet screen house.
Oversize 40 -100mm goes back through a crusher house where there are two Sandvik CH430 crushers: one for coarse material and the second for fine. There is a splitter screen and two bins, one on top of each crusher, the 40 mm in one and the oversize 40-100 mm goes into another bin which is crushed separately. That is re-fed onto the main feed conveyor, which goes up to the wet screen house comprising two double deck screens where washing takes place on both decks of each screen to ensure clean single size 10 and 20mm gravel, there is also a + 20mm re-feed conveyor return to the crusher house.
The Sandvik crushers replace the old plant’s mobile, diesel-powered crusher. They automatically power down when not needed, enabling a power saving of 132,000 kW a year. Sandvik’s ASRI control system looks after the wear rate, which can be displayed on a daily basis allowing planned changes of wear parts. Two metal detectors on the conveyors ensure anything metal is kept out of the crushers.
In the wash house the plant separates the single size material and flumes down the water/sand product into the Linatex Sand Processing and Screen Dewatering System, which washes and dewaters the sand fraction to reduce the silt content in the final product. It extracts fines using cyclone circuits and dewaters the product on a screen, achieving a10.5-11% moisture content. It includes a large effluent tank and a pump to handle the dirty water. Wash water and fines emanating from the aggregate washing and sand system are treated by the Effluent Treatment System, supplied by Haith Industrial, which provides high quality treated water that can be used by the system.
The feed of material and water is flumed down to the centre of a feed regulating sump. From the base of the sump a pump draws the slurry and feeds two sets of extended Sand Separators to maximise sand/water separation, each set feeding onto two de-watering vibration screens. Fines water from the separator is returned to the effluent tank. The underflow from the dewatering screen sumps is then re-circulated back to the regulating sump. Dirty water collected in the effluent tank is pumped into the Haith Thickener for treatment.
Effluent treatment
Wash water and silt emanating from the aggregate washing and sand system is treated by an Effluent Treatment System, supplied by Haith, which provides high quality treated water that can be used by the system.
Interlocked with the effluent delivery pump feeding the thickener delivers the pre-prepared flocculent solution stored in a multi-compartment powder system equipped with a 25 kg storage hopper. Once charged with flocculent powder the system makes up flocculent to pre-set solution strength on demand. The multi-compartment system prevents short cutting and so ensures all product is fully matured before use.
The addition of flocculent is required to achieve solids liquid separation within the thickener giving rise to a thickened slurry underflow being discharged at the base of the cone shaped vessel and clear supernatant being discharged over the weir plates fixed to the inner face of the peripheral gallery on top of the thickener. The thickener internal rake system runs continually and maximises solids compaction by releasing the entrained layers of water that may be trapped in the sludge blanket. They also ensure that the compacted solids are directed towards the cone outlet and underflow pump suction.
The clarified water flows by gravity into a new clean water storage tank fitted with two pumps, one being main feed water to the screen house and the other required for feeding high pressure water to the bottom of the thickener cone to act as a stirring agent if required.
The thickened underflow is extracted from the clarifier via a centrifugal pump, sized to manage the thickened fines. The control system links this pump via a pressure transducer within the thickener drive to continually monitoring the torque / load on the rake system, which is an indication of the fines density. Using pre-set limits on this control enables fines of a predictable, consistent specific gravity to be discharged onto the dewatering sand screens. Haith’s Autofloc in-line measurement of the incoming solids, assessing the dosing level required to maintain the water quality set during commissioning.
Explaining the combination of the Linatex and Haith systems, Mike says: “Within the product there is always some fine material, which the sand plant doesn’t take out and it ends up going back into the water system. So the Haith thickener allows the fines to coagulate together and fall to the bottom to be then pumped back onto the Linatex screens and out into the sand. Effectively it’s a closed circuit: we are recycling water all the time, which is a huge benefit. With the old plant we were producing silt or fines at the rate of approximately 250-500 tonne/month. So we would buy the product and then end up producing an unsaleable product that had to go to landfill: a lose/lose situation. By combining the Linatex plant and Haith thickener working in conjunction we are utilising the entire product that ends up back in the sand.”
Mike adds: “The other big advantage of this system is that we have a poly dosing system that is monitored consistently to give the optimum amount of flocculent to make the fines coagulate. There’s a tremendous saving in cost on that as well.”
The end result
End product is stockpiled in locations just a short travel distance for loading shovels supplying materials to Aggregate Industries. The footprints are as big as possible to eliminate double handling: the 10 and 20 mm piles are approximately 10,000 tonnes while the sharp washed sand is round about 20,000 tonnes. “The site previously had small stockpiles and we were continuously moving material,” says Mike. “Now we can load straight from stockpiles and this saves fuel and wear and tear on loading shovels. The cost saving in fuel has dropped from about 24 litres/hr down to approximately 19, purely because the shovel is running very short distances and it does not have to rush, which is a significant saving.”
Frindsbury is now a 1.2 million tonne a year plant, without having to work 24 hours a day. “We don’t have to produce as often as we did before to reach the sales target,” says Mike. “On the old plant, we worked essentially 24 hours a day to produce approximately 400,000 tonnes a year. So the new plant is extremely efficient.”
One of the other important savings we’ve found is that on the old plant, the feed hopper was a significant distance from the raw material, so we positioned the feed hoppers much closer to the ship discharge point, so the loading shovel doesn’t have to travel so far. One loading shovel (a Komatsu W500) can feed the plant at 600 tph quite comfortably.” This reduces fuel consumption by 28% and increases throughput by a factor of 2.5.
Eliminating the old mobile crushing equipment meanwhile gives further fuel savings of 75,000 litres.
Hanson has full control over the new plant, which can be started or shut down (in sequence) by pressing a single button. The computer-based control system provides full diagnostics and Hanson can control all of the plant’s numerous parameters remotely and fine tune the system. Each of the plant’s stations has a control box with internet cables coming out of it to communicate with the control room, which means adjustments can be made without the need to rewire. All the plant’s cabling is underground.
“We keep daily and running records of the water we use, belt wears on the main conveyor, the kW hours we are using as well as running totals of materials produced. This all goes into a reporting system, which gives the Directors a clear view of performance of plant through key performance indicators (KPI).”
In addition to numerous health and safety aspects, the design allows easy maintenance with walkways giving access to all areas of the whole structure, which is double-dip galvanised to marine standard. Because components have been kept predominantly to four sizes, spares inventory is minimised. The external lighting is accessible from inside the plant buildings so scaffolding towers are not required for maintenance. Internal lighting is also located at a low height to eliminate the need for ladders.
Installation was carried out in two parts: building one half of the new installation while the old plant – essentially mobile kit mounted on stilts – continued operating until it was time to shut it down. The build commenced in May 2009, the old plant was pulled down in September 2009 and commissioning of the new plant commenced around Mid-April 2009.
Mike concludes “The new plant is far more efficient, requires fewer staff, maintenance is easier and safer, and the access issues we had in the plant have all been eliminated.”
For further information about Hanson UK and their operations then click here
Cavalier Road
Heathfield Industrial Estate
Newton Abbot
Devon
TQ12 6TQ UK
Phone: 01626 83 43 10
Fax: 01626 83 46 81
Company No. 1549267
VAT No. 927 3238 18
Cavalier Road
Heathfield Industrial Estate
Newton Abbot
Devon
TQ12 6TQ
Phone: 01626 83 43 10
Fax: 01626 83 46 81
Company No. 1549267
VAT No. 927 3238 18
Job Vacancies Available
|